Contact: Claire
Email:sales3@mooreplc.com
Tel/whatsapp:+86-18150117685
Collaborative robots are cheap and easy to program and debug. They are increasingly appearing in manufacturing, packaging, food and beverage manufacturing, and are springing up the industry.
Recently, an automotive component supplier used collaborative robots to achieve manufacturing innovation. The company is Comprehensive Logistics, which manufactures suspensions, powertrains and interior components for two of North America's largest automotive companies. The factory needed a reproducible way to inspect the engine bracket subassembly line and found a solution on the Unirox robot.
Automated inspection of the engine bracket subassembly is a challenge, including a critical steering harness harness connector that also needs to be synchronized with the high capacity of the line while ensuring proper connection to the electrical connectors in the harness.
Initially, car manufacturers used a fixed multi-camera system, but could not position the camera in a compact position. The data collected by the fixed camera system was not so complete. The company also tried probe robots and manual detection programs. The program did not improve repeatability.
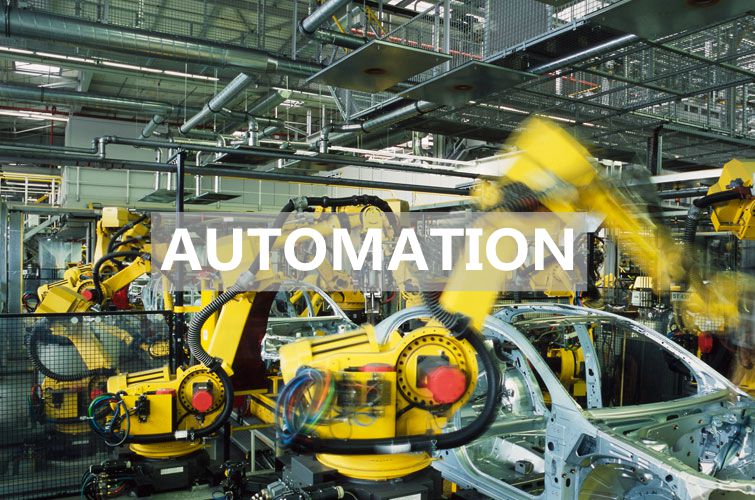

The new solution uses the largest collaborative robot UR10 and Keyence's CV-X camera, which is part of the CA-HX200C LumiTrax vision system for navigating sub-assembly units and providing repeatable test results. The ceiling-mounted UR10 cooperating robot moves quickly between checkpoints, allowing the CV-X camera to capture each connected image before the coordinating arm retracts to its original position and then wait for the next component to be inspected.
During the inspection of the subassembly, each image is immediately displayed on the screen next to the robot, while the second screen with the engine mount map shows that each checkpoint is completed with a green or red check mark to indicate pass/fail . The company's Manufacturing Execution System (MES) collects pass/fail data and stores this information on the camera's memory card for two days.
Diesel and gas engine engine mounts have 11 and 9 checkpoints, respectively, and any engine product needs to be identified. Identifying different engine types and other critical data requires the robot and camera system to communicate with the assembly line programmable logic controller (PLC) via Industrial Ethernet.
The system will run the first pass at all checkpoints, and if one parameter fails, the system will reset. Each station has a 60-second takt time on the assembly line, the inspection cycle time is approximately 48 seconds, and the UR10 cobot takes approximately 32 seconds. This setting allows the rerun time to fail and the entire assembly line does not stop.
The overall inspection time is critical because the integrated logistics receives instant (JIT) orders from the car manufacturer. In the past three years, contract manufacturers have received more than 600,000 orders for sub-assembly related engine products.